La simulación de máquinas crea una representación virtual de un programa CAM que refleja exactamente lo que ocurrirá en la máquina CNC. Básicamente, crea un modelo del proceso de corte que los usuarios pueden seguir en tiempo real. Muestra la pieza de trabajo, las herramientas y los accesorios, así como la forma en que interactúan entre sí, resaltando cualquier punto en el que se cometa un error. Este blog te guiará a través de los tres mayores beneficios de usar la simulación de máquina al programar tus piezas CNC.
Experimentar con diferentes estrategias de fabricación para encontrar el proceso más eficiente
Con la simulación de máquina, no es necesario ocupar una máquina o desperdiciar material realizando pruebas. Los usuarios pueden determinar qué enfoque de maquinado produce las piezas más rápidas y de mayor calidad con solo hacer clic en unos botones.
Lo primero que los programadores deben analizar en su simulación es la sujeción. ¿Es esta opción la mejor disponible para esta pieza en particular? ¿Hay alguna forma de cambiar la sujeción para eliminar una o varias reposiciones?
Después de decidir sobre una sujeción, pueden generar su código. En casi cualquier programa, hay margen de mejora. A menudo, múltiples trayectorias de herramientas se pueden integrar en una sola. Considera la estrategia de trayectorias Dynamic OptiRough. Reemplaza múltiples enfoques de desbaste optimizando los avances, velocidades y ángulos para eliminar el material más rápidamente y de manera segura. A veces, se requiere una estrategia de maquinado completamente nueva. Para una pieza que requiere una larga lista de configuraciones, un programador puede experimentar con el maquinado 3+2. Este enfoque es un trampolín hacia el maquinado multieje y puede reducir drásticamente los tiempos de ciclo. En cualquier caso, el usuario puede crear y aplicar nuevos enfoques, por más audaces que sean, y ver exactamente cómo se desarrollarán sin poner en peligro nada.

Detectar colisiones entre tu material, herramienta y componentes de la máquina
Las características de simulación de Mastercam analizan el material en bruto, cabezales, torretas, mesas, husillos, herramientas de corte, cambiadores de herramientas y accesorios durante cada paso del maquinado planificado. Toma todos los datos cuidadosamente seleccionados sobre cada componente y los utiliza para mapear con precisión dónde estará cada uno. A estas alturas, sabes lo importante que es evitar colisiones en la máquina. Pero este paquete de Simulación va más allá y también verifica colisiones con los componentes del material de stock y la sujeción. Incluso una pieza con las tolerancias más amplias es inútil si se le hace una gran marca durante el maquinado debido a un error de programación.
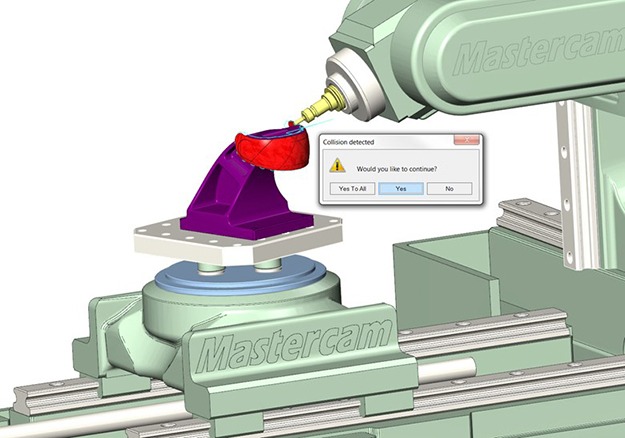
Encontrar errores en tu código, no en la máquina
Se dedica mucho tiempo y esfuerzo a optimizar la programación, reducir el desgaste de las herramientas y mantener las máquinas calibradas. Pero la verdad es que todo este trabajo no sirve de nada si la máquina colisiona. Cuando algo en el proceso de maquinado sale mal, el peor lugar para que suceda es en la máquina. Las máquinas CNC cuestan, como mínimo, varios miles de dólares. Son inversiones. Si una se estrella debido a que una herramienta de corte colisiona con ella, puede ser desastroso para un taller. No solo el fabricante perderá tiempo que podría haberse dedicado al maquinado, sino que también tendrá que pagar para reparar o reemplazar la máquina.
Con un paquete completo de simulación de máquinas, los problemas se detectan mientras la pieza aún se está programando en el software CAM. La herramienta de simulación dentro del software CAD/CAM de Mastercam señala a los usuarios no solo si se detecta una colisión, sino también si se detecta una colisión próxima. Luego, con solo unos clics, los programadores pueden resolver los problemas y seguir trabajando. Cuando se encuentran errores antes de que la pieza vaya a la máquina, la única pérdida es el tiempo. Y, aun así, la pérdida es mínima.

Da clic para iniciar una conversación en vivo con nuestros expertos o comunícate al para más información.